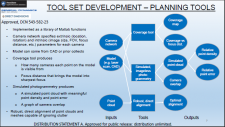
Download Members: $0.00 Non‑Members: $75.00 |
Buy Now |
Publication Details
Published Date: | |
---|---|
Authors: | David, Rearick, Marrara, Thaddeus, Morgan, John,Ortman, Robert, Rearick, West, James Craig, Albanese, Dominic, Raphael, Michael, Tardif, Susan |
Download Format: |
Abstract
The shipbuilding industry has a requirement for periodic in-process dimensional checks that are performed by experienced survey crews. To reduce cycle time and survey labor, there is a desire for an automated metrology solution that can be executed by non-metrology tradespersons while providing comparable accuracy (1/16” RMS) and data products. The project team explored a broad range of metrology instruments and physical automation approaches before identification of targetless photogrammetry as the optimum solution.
Trade studies of photogrammetry software, cameras, and point cloud analysis software were conducted to identify solutions that could be integrated into an automated workflow while meeting accuracy requirements. Modeling tools were developed that enabled offline planning of camera position and pose matrices that would render point cloud fidelity adequate for extraction of accurate coordinates at key points on the ship structure.
Testing was conducted with representative ship structure using a DSLR camera and overhead cable rig to validate the photogrammetric solution. PolyWorks was utilized to extract coordinates at key locations on the structure and results were compared to conventional survey results.
Options for automating the collection of imagery were limited by safety considerations, physical and environmental constraints in the assembly building, and a requirement to minimize disruption of existing operations. Use of a large form factor drone with indoor navigation was considered but recent advances in autonomous compact drones proved to be a more viable solution.
Additional testing was conducted utilizing a Skydio X2D drone, Reality Capture, Zephyr, and PolyWorks.
The presentation will discuss the objectives and requirements, exploration of trade studies, photogrammetry test results, small drone photogrammetry test results, and data workflows. An emphasis will be placed on lessons learned, current state of the art technology, and expectations for future capabilities.