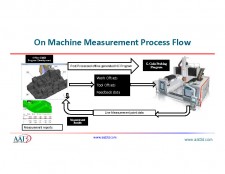
Download Members: $0.00 Non‑Members: $75.00 |
Buy Now |
Publication Details
Published Date: | |
---|---|
Citation: | Thomas Schadegg, Lockheed Martin Aeronautics, Applications Engineer |
Abstract
The Fastener Measurement Tool (FMT) project for F-35 is being nominated. This groundbreaking project took extensive advanced metrology system development to achieve an accurate and easy to use gauge for measuring filled and unfilled fastener profile relative to the aircraft skin.
In 2012, Lockheed Martin’s Manufacturing Technology engineers began brainstorming and evaluating methods to more accurately measure fastener features on contoured surfaces as opposed to visual inspection, legacy dial gauges, and single line laser metrology systems. These legacy systems required extensive training, lengthy measurement time, and were highly subject to interpretation by the user. The difficulty of using these methods was exponentially compounded on contoured surfaces and one of the key drivers of this development. Legacy systems were slowing down the production line, therefore this development was identified as essential to meeting F-35 rate requirements.
Government and internal funds supported the development of a tool that would revolutionize the way fasteners are inspected. Eventually, a handheld advanced laser profilometer metrology system consisting of 99 laser lines was down selected. In order to meet production tolerances, the tool required substantial accuracy in a package that is as easy to use as selecting a function and pulling the trigger. The final system design was completed and tested from 2015-2017. The FMT was fully implemented into production on October 30, 2017. The system reduces touch labor 50%, improves measurement accuracy, and increases product quality.
This presentation will discuss requirements definition (what drove the need for a new measurement system), technical development of the device, and advantages that the device brought to production once implemented.