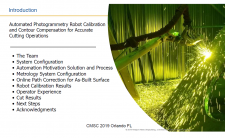
Download Members: $0.00 Non‑Members: $75.00 |
Buy Now |
Publication Details
Published Date: | |
---|---|
Download Format: | |
Citation: | Whaley, Donald, Newport News Shipbuilding, Donald.D.Whaley@hii-nns.com Seiler, Steven, New River Kinematics, steve.seiler@kinematics.com Sandwith, Scott, New River Kinematics, scott@kinematics.com Hanley, Harry, Geodetic Systems Inc., harry@geodetic.com |
Abstract
The use of metrology to extend the accuracy and working volume of an articulated robotic system has many applications in manufacturing. This paper documents and provides test results for a project where the requirement is to control the accuracy of large beveled holes cut into contoured 1–3 in.- thick steel plate over a working volume of 70-in. Cut-paths are computed from CAD models of the desired beveled cutouts and are used to command a FANUC M-710iC45M robot. The FANUC robot employs an oxy-fuel torch to perform the actual cuts. The solution uses a series of photogrammetric techniques throughout the process. The photogrammetry system uses four high precision cameras on electronic pan-tilt-roll motors on adjustable stands to help ensure line-of-sight to the cutting volume, to the reference targets, and to the torch head. An extrinsic and intrinsic robot calibration is computed prior to cutting each hole. Test results show the calibration improved the robot’s positional accuracy from a max error 0.112 in. and an average error of 0.042 in. to a max error of 0.033 in. and an average error of 0.011 in. Cuts can span from 1 to 6 ft in width and height. The cut and calibration depth can extend 2 to 3 ft across the width and height of the cut.