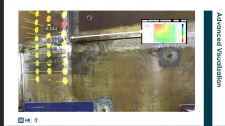
Download Members: $0.00 Non‑Members: $75.00 |
Buy Now |
Publication Details
Published Date: | |
---|---|
Authors: | Steve Seiler, Justin Novak |
Download Format: |
Abstract
This paper will detail the development, testing, and integration efforts associated with a Near Real Time Weld Distortion Metrology System installed at Newport News Shipbuilding. This system was developed as a collaborative effort between Metrologists at NNS and the Custom Solutions division of New River Kinematics, part of Hexagon Manufacturing Intelligence. NNS needed to continuously monitor the shape of a submarine hull as it deforms due to heat stress from welding. The goal was to provide easily interpreted and instantly available reports so that tradespeople can manage the distortions before they could become problems. The solution also needed to run for months at a time in a challenging manufacturing environment and be as autonomous as possible to keep metrology experts available for other demanding shipyard activities.
New laser scanning technology (3 Leica ATS600s) paired with sophisticated scripting through SpatialAnalyzer’s Measurement Plan language have allowed the implementation of some new approaches to high accuracy, large volume, non-contact metrology. Contrast targets were utilized in lieu of SMR nests for the control network. Initial tie-in required only one video-guided observation for each live instrument, and no operator intervention for subsequent instrument locations. The part’s surface point grid was measured with a technique that ensures consistent comparison between measurement epochs that was available only for Laser Radar instruments previously. Scripting allowed for simultaneous measurements of three instruments to reduce the overall measurement time. Consistent measurement methods and deviation image captures together with a customized reporting application allowed for easily comprehended trend analysis and error visualization.
This paper will discuss how the overall system design to meet the requirements of continuously measuring and reporting autonomously in a construction environment, as well as the novel approaches taken to establish and maintain the instrument network, methods used to resolve data into highly repeatable data sets, and, ultimately, how the data is presented to and used by the customer. The new technique developed for the observation of contrast targets with the Leica ATS600 will be detailed, as well as preliminary results for the accuracy of acquiring these centers and the influence of variables like angle of incidence, distance to target, and angle of scan pass.