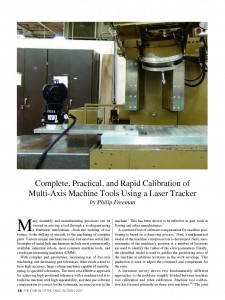
Download Members: $0.00 Non‑Members: $75.00 |
Buy Now |
Publication Details
Published Date: | |
---|---|
Authors: | Philip Freeman |
Company: | CMSC |
Print Format: | Technical Paper |
Citation: | Philip Freeman, "Complete, Practical, and Rapid Calibration of Multi-Axis Machine Tools Using a Laser Tracker," The Journal of the CMSC, Vol. 2, No. 2, Autumn 2007 |
Abstract
Many assembly and manufacturing processes can be viewed as moving a tool through a workspace using a kinematic mechanism; from the welding of car bodies, to the drilling of aircraft, to the machining of complex parts. Various unique mechanisms exist, but most are serial link. Examples of serial link mechanisms include most commercially available industrial robots, most common machine tools, and coordinate measuring machines (CMM). With complex part geometries, increasing use of five-axis machining, and decreasing part tolerances, there exists a need to have high-accuracy, large-volume machines capable of manufacturing to specified tolerances. The most cost-effective approach for achieving high positional tolerance with a machine tool is to build the machine with high repeatability, and then use software compensation to correct for the systematic accuracy errors in the machine. This has been shown to be effective in past work at Boeing and other manufacturers. A common form of software compensation for machine positioning is based on a three-step process. First, a mathematical model of the machine’s motion errors is developed. Next, measurements of the machine’s position at a number of locations are used to identify the values of the error parameters. Finally, the identified model is used to predict the positioning error of the machine at arbitrary locations in the work envelope. This prediction is used to adjust the command and compensate for the error.