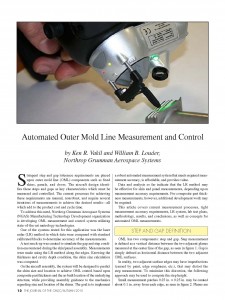
Download Members: $0.00 Non‑Members: $75.00 |
Buy Now |
Publication Details
Published Date: | |
---|---|
Authors: | Ken R. Vakil, William B. Louder |
Company: | CMSC |
Print Format: | Technical Paper |
Citation: | Ken R. Vakil, William B. Louder, "Automated Outer Mold Line Measurement and Control," The Journal of the CMSC, Vol. 5, No. 2, Autumn 2010 |
Abstract
Stringent step and gap tolerance requirements are placed upon outer mold line (OML) components such as fixed skins, panels, and doors. The aircraft design identifies these steps and gaps as key characteristics which must be measured and controlled. The current processes for achieving these requirements are manual, nonrobust, and require several iterations of measurements to achieve the desired results—all which add to the product cost and cycle time. To address this need, Northrop Grumman Aerospace Systems (NGAS) Manufacturing Technology Development organization is developing OML measurement and control system utilizing state-of-the-art metrology technologies. One of the systems tested for this application was the laser radar (LR) method in which data was compared with standard calibrated blocks to determine accuracy of the measurements. A test mock-up was created to simulate the gap and step condition encountered during the skin/panel assembly. Measurements were made using the LR method along the edges. Knowing the thickness and cavity depth condition, the shim size calculation was computed. On the aircraft assembly, the system will be designed to predict the shim size and location to achieve OML control based upon composite part thickness and the as-built location of the underlying structure, while providing assembly guidance to the mechanics regarding size and location of the shims. The goal is to implement a robust automated measurement system that meets required measurement accuracy, is affordable, and provides value. Data and analysis so far indicate that the LR method may be effective for skin and panel measurements, depending upon measurement accuracy requirements. For composite-part thickness measurements, however, additional development work may be required. This article covers current measurement processes, tight measurement accuracy requirements, LR system, lab test plans, methodology, results and conclusions, as well as concepts for automated OML measurements.