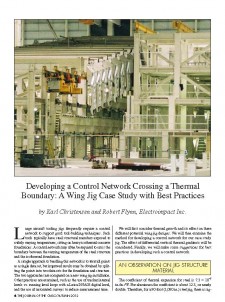
Download Members: $0.00 Non‑Members: $75.00 |
Buy Now |
Publication Details
Published Date: | |
---|---|
Authors: | Karl Christensen, Robert Flynn |
Company: | CMSC |
Print Format: | Technical Paper |
Citation: | Karl Christensen, Robert Flynn, "Developing a Control Network Crossing a Thermal Boundary: A Wing Jig Case Study with Best Practices," The Journal of the CMSC, Vol. 7, No. 2, Autumn 2012 |
Abstract
Large aircraft tooling jigs frequently require a control network to support good tool-building techniques. Such tools typically have steel structural members exposed to widely varying temperatures, sitting on heavy isothermal concrete foundations. A control network may often be required to cross the boundary between the varying temperature of the steel structure and the isothermal foundation. A simple approach to bundling this network is to treat all points as a single data set, but improved results may be obtained by splitting the points into two data sets for the foundation and structure. The two approaches are compared on a new wing jig installation. Other practices are examined, such as the use of tracker internal levels vs. running level loops with a Leica DNA03 digital level, and the use of automated surveys to reduce measurement time. We will first consider thermal growth and its effect on three different potential wing jig designs. We will then examine the method for developing a control network for our case study jig. The effect of differential vertical thermal gradients will be considered. Finally, we will make some suggestions for best practices in developing such a control network.