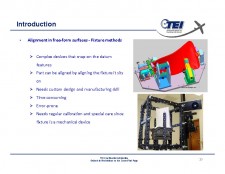
Download Members: $0.00 Non‑Members: $75.00 |
Buy Now |
Publication Details
Published Date: | |
---|---|
Citation: | Güray Akbulut, TEI - TUSAŞ Engine Industries, Senior Team Leader Soner Ören, TEI - TUSAŞ Engine Industries, Lead Engineer Ezgi Uğur Solakoğlu, TEI - TUSAŞ Engine Industries, Lead Engineer Çağdaş Şen, TEI - TUSAŞ Engine Industries, Engineer |
Abstract
Turbine blade, which is a key component in gas turbine applications, has complicated free-form surfaces and tight geometric tolerances due to increasing efficiency and performance requirements of power systems. Therefore its inspection process is a very critical task both for the performance and reliability. This complex inspection process is being achieved by direct computer-controlled systems like coordinate-measuring machines or optical 3D measurement systems. For both systems, complexity of the inspection starts from the first spatial identification of the part to the inspection system. 6-point alignment, best-fit methods and measurement fixtures are some alignment methods for the establishment of the relationship between the machine and the object. Different alignment methods and different inspection systems offer different accuracy, measurement time and ease of implementation.
This paper will present an alignment method that synthesizes the touch trigger probe and the non-contact laser scanner both mounted on a coordinate-measuring machine. A turbine blade with a complex free-form blade profile and a fir-tree shaped root section is used for the alignment. Rough alignment is conducted with the non-contact laser scanner by best fitting the point cloud onto the reference model. Rough alignment is followed by a fine alignment, which is conducted with touch trigger probe using the iterative 6-point alignment. Then the alignment procedure is repeated by only using the touch trigger probe with the same set of parameters for the iterative 6-point alignment. The aim of this work is to examine the feasibility of uniting the better accuracy of touch probe and the measurement speed of non-contact laser scanner for alignment on a free-form surface.