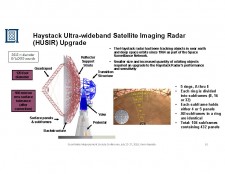
Download Members: $0.00 Non‑Members: $75.00 |
Buy Now |
Publication Details
Published Date: | |
---|---|
Citation: | E. Kushnir, R. Karadayi ,W.Clark, A., C.Affer, A.Naga |
Abstract
Modern super precision tuning centers have to provide accuracy in lower range of diamond turning machines (cylindricity under 1-2 micron) and high productivity, that diamond turning machines are not able to delivery because of their design limitations. High accuracy may be achieved if compensation of error will be compute based at feedback from results of part dimensions and profile measurement. At this moment are known systems that provide dimensional and sometimes profile feedback by results of measurement performed outside of cutting envelope of a turning center (lathe). For super precision turning centers with relative short duty cycles this approach is not effective. Super precision of turning center allows using it guide ways system as support for measuring device and perform in envelope measurement of part profile and dimensions. Information obtained during this measurement is used for compensation of errors that are correlated to variation in cutting force as function of tool wear and variation of parts material characteristics in the batch.
This type of compensation has sense only when increase of turning center accuracy by any mechanical means will be too expensive or not achievable. Using an in envelope measuring system for error compensation may be justified only if machining center feed system has ability to perform small steps that are at least 0.1- 0.2 micron that is 5-10 times less that of required profile accuracy in the range of 1-2 micron.
In CNC part profile is represented by data saved in CAD/CAM system as a set of standard features or points representing part profile and set of commands (CNC program) for it machining. Additional CNC functions include position and straightness error compensation. In error compensation applications grid step may be defined by CNC programmer as function of part size, required accuracy, and available memory that is allocated for additional functions performed by CNC. Usually up to 500-1000 points for axis is allocated for position and straightness compensation. Modern CNC performs straightness compensation movements in direction normal to coordinate axis and only in points that belong to it compensation grid Position compensation is performed in the same points but along the coordinate axis.
It is obvious that accuracy of profile compensation will be affected by compensation grid step, and consequently by number of points involved. From other point of view, required grid step is function of profile waviness that will define required compensation accuracy. In any case step of the grid used for compensation will be bigger that minimum size of grid used by CNC during machining. That means that part representation for profile error compensation has to be a sub set of points used in it CNC representation. Because CNC profile representation is obtained during machining from CAD/CAM data for purpose of automatic error compensation the same CAD/CAM data has to be transformed to represent part profile through a set of points with coordinates that belong to grid used for compensation – to set points in which CNC will perform computed compensation movements. Thus this compensation movement is based at CNC position and straightness compensation functions and it will not alter original machining program.
Compensation value in every of these points has to be compute based at part profile measurements. A profile measurement program with certain (optimized by accuracy and productivity criteria) amounts of measurements points performs measurement in subset of chosen set of compensation points that represent part profile. The obtained subset of points is used to perform profile measurement. For any giving profile programs that develop set of compensation points and subset of points for measurement have to be run only one time before machining the part.
After cutting is performed the machined profile has to be measured in chosen points.
All obtained in measurement error data (measurement points of type (Zf, X) and (Z, Xf)) are used for error approximation in compensation points not included in measured subset in both directions. In this case even if in some points measured error value in one of directions will not be used for compensation it still is used for error approximation. This way all profile measurement data are used in computing to increase calculation accuracy.
The compensation values have to be compute in direction normal to part profile. Projections of the compute normal error (error vector along normal to profile) at the Z and X axes are used for compensation. This approach allows by definition to make compensation of part profile - by the direction normal to profile not tangents to it.
Requirements to Enhance Super Precision Turning Machining Centers
The Enhance Super Precision Turning Machining Center that will be able to machine hard materials (RC 55 and higher) in the range of turning accuracy 1-2 micron has to include:
- Machine tool with high stiffness of the cutting loop (the variation in cutting force from pass to pass develop displacement in cutting zone 5-10 times less than required accuracy);
- Machine tool with slides that have ability to perform very small steps (less than 0.1 micron) with high repeatability of motion;
- Measurement equipment that allow to perform measurements with accuracy 5-10 times better than required accuracy;
- Measurement program that allow to perform measurement in defined points along part profile, developed by machine CNC control;
- Compensation methodology that does not require cutting program modification;
- Compensation program that will compute compensation values in chosen statically defined grid points (compensation points) of machine tool coordinate system;
- Interfaces between Measurement program, Compensation program and CNC that allow for no interrupted flow of data between different components of machine tool and compensation system without operator intervention.
Turning center model T51 as representative of family of Super Precision turning centers (models T42, T51, T65) satisfies all mentioned requirements. The T51 turning center is equipped with FANUC I-31 CNC. This machine has ability to perform small step of 0.1 micron and has very high level of repeatability. Machine accuracy was checked by cutting of aluminum cylinder with 75 mm radius and length of 250 mm. Machine has straightness in cutting envelop less than 0.2 micron and perpendicularity less than 0.2 micron/meter.
Marposs measurement sensor is set up at the same slides that cutting tool. Accuracy of this sensor is in the range of 0.25 micron. Measurement of machined profile is performed when slide is moving along different parts of guideways then during cutting. For this reason the measurement motion has to be correlated with cutting motion to deliver adequate data. This correlation was performed by measurement of control profile in X and Z direction and electronic compensation of measurement pass errors to the extent that results of measurement profile at Roundcom and at the machine tool are close with accuracy of 0.2 micron.
Software needed to represent part profile in grid points and perform required measurements and calculations was developed as extension of AAT3D CappsNC In Process Measurement program. FOCUS support interface of FANUC CNC was used to insure continuous flow of data between CNC, CappsNC, and it extension at all steps of profile measurements, analyses, and cutting.
The developed compensation procedure and developed software were verified by cutting a part of sphere at T51 Super precision Machining Center.