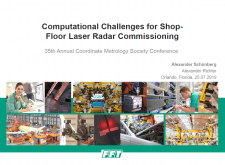
Download Members: $0.00 Non‑Members: $75.00 |
Buy Now |
Publication Details
Published Date: | |
---|---|
Download Format: | |
Citation: | Alexander Schönberg – FFT –Sensor Technology; Alexander Richter – FFT –Sensor Technology |
Abstract
Optical metrology technologies are increasingly used in the manufacture of automobiles for absolute measurements. Laser radar uses a common principle of optical metrology, namely the deflection of a laser beam through an optical system and the evaluation of the light path. By attaching the laser radar to a robot, the beam can be placed at positions using a kinematic model within the measurement volume. A steerable single beam system that requires an unobstructed line of sight and complies with length and angle constraints is simulated to determine viewpoint candidates.
A development scenario will be implemented with a framing stage vehicle, a Fanuc M900 robot-mounted Nikon Metrology MV331-HS, and a network of 28 tool balls. Laser tracker measurements are provided as an absolute comparison reference. The network is measured with 880 observations to calibrate base, tool and axis deviations of the robot as well as kinematic deviations of the laser radar. The calibrated simulation generates measurement programs for measuring and optimizing 1028 visible features with 9283 observations. Bundling is done internally and compared to laser tracker measurements. Statistical evaluations are presented and an outlook on scenarios in series production is applied.