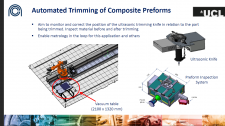
Download Members: $0.00 Non‑Members: $75.00 |
Buy Now |
Publication Details
Published Date: | |
---|---|
Authors: | T.Legleu2, M.Mainwaring1, A.Metherell1, A.Ola1, V.Pawar2, C.Richards2, S.Robson2, B.Sargeant2, P.Saunders1 and R.Smith2 |
Download Format: |
Abstract
Trimming of composite preforms requires the accurate cutting of 2D and 3D high value components as part of a wider manufacturing chain. The operation needs to be performed rapidly and reliably with a fast high quality cut to avoid process bottlenecks and minimise waste.
The UK National Composites Centre (NCC) is expert in robotic ultrasonic knife cutting over small, medium, and large volume components with the capability to trim complex shapes. However, after a changeover, or before an important cut, the question needs to be asked: “Is the robot about to cut in the right position and orientation?”
This presentation explores the metrology developed through a project initiated at the NCC to further mature a low-cost photogrammetric system developed at University College London and reported at CMSC in 2021. Project objectives are to integrate and subsequently demonstrate photogrammetric robotic control on the ultrasonic trimming process.
A network of off-the-shelf low-cost cameras and lenses were deployed around the working area to form a measurement system capable of 6DoF tracking a custom ultrasonic knife end-effector in relation to a cutting table (Figure 1). Targets were mounted close to the knife tip whilst maintaining line of sight to as many cameras as possible in all poses and orientations of the knife during the cutting process. This information is communicated to the robot controller so that the path can be adjusted. A customised knife mount was developed to allow for precise setting of the knife orientation to minimise downtime during blade changes.
Whilst validation of knife tip location is on-going, preliminary results are that tracking capability meets or exceeds a 0.2mm positional capability over the test cutting space. These data will be expanded on in the presentation referencing knife trajectories established from system validation tests.
This project was supported by funding from the NCC’s annual Technology Pull-Through programme with supports the transfer and further development of academic technologies into industrial and commercial environments and by the UK’s Royal Academy of Engineering which sponsors the UCL/Airbus Chair in Large Volume Metrology.