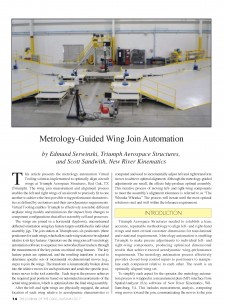
Download Members: $0.00 Non‑Members: $75.00 |
Buy Now |
Publication Details
Published Date: | |
---|---|
Authors: | Edmund Serwinski, Scott Sandwith |
Company: | CMSC |
Print Format: | Technical Paper |
Citation: | Edmund Serwinski, Scott Sandwith, "Metrology-Guided Wing Join Automation," The Journal of the CMSC, Vol. 12, No. 2, Autumn 2017 |
Abstract
This paper presents the metrology automation Virtual Tooling solution implemented to optimally align aircraft wings at Triumph Aerostructures-Vought Aircraft Division (Triumph). The Wing Join measurement and alignment process enables Triumph to ensure the left and right wings are precisely fit to one another to achieve the best possible wing performance characteristics. Virtual Tooling enables Triumph to effectively assemble different airplane wing models and minimizes the impact changes to component configurations have on assembly cell and processes. The wings are joined in a laydown unconstrained deflected orientation using key feature targets established in individual assembly jigs. The join station at Triumph uses six positioners (three positioners for the LH Wing & three positioners for the RH Wing) which allow each wing section to be adjusted relative to their key features. Operators use the Wing Join Cell’s Metrology Automation Software to sequence two online laser trackers through the measurement of key points on critical wing features. The key feature points are optimized and the resulting transform is used to determine specific sets of incremental 6D moves (e.g., steps) to join the wings. The transform is kinematically decoupled into the relative moves for each positioner and sends the specific positioner moves to the tool controller. Each step in the process achieves goal positions based on automated measurements of the actual wing position and the optimized into the final wing assembly. After the left and right wings are physically engaged, the actual location of each wing relative to aerodynamic characteristics is computed and used to incrementally adjust left and right transform moves to achieve optimal alignment. While the metrology guided adjustments are small, the effects help produce optimal assembly. This iterative process of moving left and right-wing components to meet the assembly’s alignment tolerances is referred to as “The Whonka Whonka.” The process will iterate until the most optimal solution is met and well within the tolerance requirement.