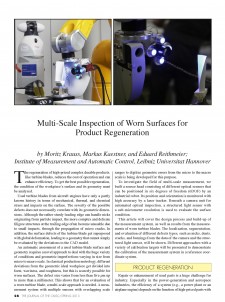
Download Members: $0.00 Non‑Members: $75.00 |
Buy Now |
Publication Details
Published Date: | |
---|---|
Authors: | Moritz Krauss, Markus Kaestner, Eduard Reithmeier |
Company: | CMSC |
Print Format: | Technical Paper |
Citation: | Moritz Krauss, Markus Kaestner, Eduard Reithmeier, "Multi-Scale Inspection of Worn Surfaces for Product Regeneration," The Journal of the CMSC, Vol. 8, No. 1, Spring 2013 |
Abstract
The regeneration of high-priced complex durable products, like turbine blades, reduces the cost of operation and can enhance efficiency. To get the best possible regeneration, the condition of the work piece’s surface and its geometry must be analyzed. Used turbine blades from aircraft engines have only a partly known history in terms of mechanical, thermal, und chemical stress and impacts on the surface. The severity of the possible defects does not necessarily correlate with its geometric dimensions. Although the rather sturdy leading edge can handle nicks originating from particle impact, the more complex and delicate filigree structures at the trailing edge often become unusable due to small impacts, through the propagation of micro cracks. In addition, the surface defects of the turbine blade get superposed with global deformation, leading to a geometry that cannot simply be evaluated by the deviations to the CAD model. An automatic assessment of a used turbine blades surface and geometry requires a novel approach to deal with the huge variety of conditions and geometric imperfections varying in size from micro- to macro-scale. In classical production metrology, different deviations from the geometric ideal work piece get divided into form, waviness, and roughness, but this is scarcely possible for worn surfaces. The defect size varies from less than five ?m up to more than a millimeter. This shows that for an evaluation of a worn turbine blade, a multi-scale approach is needed. A measurement system with multiple sensors with overlapping scale ranges to digitize geometric errors from the micro to the macro scale is being developed for this purpose. To investigate the field of multi-scale measurement, we built a sensor head consisting of different optical sensors that can be positioned in six degrees of freedom (6DOF) by an industrial robot. Its position and orientation is monitored with high accuracy by a laser tracker. Beneath a camera unit for automated optical inspection, a structured light sensor with a sub-micrometer resolution is used to evaluate the surface condition. This article will cover the design process and build-up of the measurement system, as well as results from the measurements of worn turbine blades. The localization, segmentation, and evaluation of different defects types, such as nicks, dents, cracks, and burnings from the data of the camera and the structured light sensor, will be shown. Different approaches with a variety of calibration targets will be presented to demonstrate the calibration of the measurement system in a reference coordinate system.