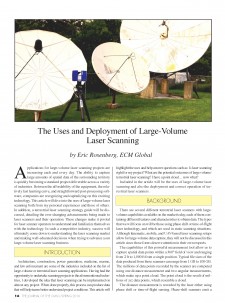
Download Members: $0.00 Non‑Members: $75.00 |
Buy Now |
Publication Details
Published Date: | |
---|---|
Authors: | Scott Sandwith |
Company: | CMSC |
Print Format: | Technical Paper |
Citation: | Scott Sandwith, "Production Line Robot Calibration Verification Test Results," The Journal of the CMSC, Vol. 11, No. 1, Spring 2016 |
Abstract
This article presents test results for a production line robot calibration solution. The tests were performed to evaluate aerospace performance capabilities of dressed robots (i.e., robots outfitted with tooling, cables, and ancillary support accessories) for the shop floor. Off-the-shelf robotic systems are repeatable but generally not accurate enough for aerospace applications. For dressed robots in a production cell to meet tight tolerances, they can be taught each position (which can be time-consuming and inflexible), or they need to be calibrated and compensated for in the production environment, under load and within the application’s working volume. In this project, application engineers from New River Kinematics (NRK) of Williamsburg, Virginia, investigated NRK’s SpatialAnalyzer Robot Calibration Appliance (SARCA) solution. The purpose was to evaluate whether the calibration(s) can deliver zone calibrations to meet typical aerospace requirements. SARCA is a hardware and software system that allows users to network a precise metrology system and a robot controller, and it works in conjunction with a robot program to automate measurements of robot poses within different volumes and loads. SARCA then creates new kinematic parameter sets for different loads and volumes (e.g., Cal_Id1, Cal_Id2, …, Cal_Idn) for the robot—in this case, an ABB 6640 robot with an IRC5 ABB controller. After calibration and compensation, the metrology system is taken out of the loop and the robot can run using one of the new kinematic models. We performed the SARCA compensation and then ran a verification program, and discovered that the volume was similar but verification poses and positions were different from the compensation program. Results of this experiment were as follows: Under the robot’s Absolute Accuracy (ABSACC) control (provided by ABB), the maximum error was 0.046 in., and the average error was 0.025 in. Under SARCA control, on the other hand, the maximum error was just 0.009 in., and the average error was 0.005 in. These data were developed over a robot working space consisting of a 40 in. × 40 in. × 80 in. volume. Once calibrated and compensated for, SARCA’s calibrations are useable from within the native robot programming environment. The solution enables the production process to utilize offline programming and deliver tighter tolerance results within production.